汽车用行星减速机的节能效果主要源于其结构设计、材料优化与智能控制技术的结合,以下是其核心节能机制及应用场景分析:
一、节能核心原理
高效传动减少能量损耗
行星减速机采用多齿轮均载设计,传动效率可达95%-98,相比传统蜗轮蜗杆减速机(效率约70-85%),能量损耗降低10-15%。例如,汽车电动助力转向系统(EPS)采用行星减速机后,能耗减少约30%。
轻量化设计降低整车能耗
行星减速机体积较传统减速装置缩小30%,重量减轻25%,降低汽车动力系统负荷。
在新能源汽车电驱动系统中,轻量化设计可使百公里电耗减少0.5-0.8kWh。
动态负载匹配优化能耗
智能控制模块通过实时监测驾驶工况(如加速、爬坡),动态调整传动比,避免无效功率输出。例如,与伺服电机协同工作时,可提升能量利用率12%-18%。
二、节能技术实现路径
技术方向 具体措施 节能效果
材料优化 高强度合金钢+真空淬火工艺 摩擦损耗降低20%,寿命延长30%
润滑系统升级 纳米级润滑剂+循环油冷系统 运行温度下降15℃,能耗减少8%
齿轮啮合精度提升 摆线轮齿廓精度达IT3级 传动误差≤1弧分,效率提升5%-7%
智能控制集成 AI动态负载预测算法 综合能耗降低10%-15%
三、典型汽车应用场景
电动助力转向系统(EPS)
行星减速机通过95%以上的传动效率,将电机输出扭矩精准传递至转向机构,相比液压助力系统节能50%以上。
新能源车电驱动系统
在混合动力汽车(HEV)中,行星减速机与永磁同步电机配合,能量回收效率提升至92%。
纯电动车(EV)减速器采用行星结构,高速工况下续航里程增加5%-8%。
自动变速器(AT/DCT)
行星齿轮组通过多片离合器动态切换速比,换挡过程能耗降低30%,综合传动效率达89%。
四、节能效益量化对比
车型/系统 传统方案能耗 行星减速机方案能耗 节能率
燃油车转向系统 0.8-1.2kW 0.4-0.6kW 40%-50%
电动车减速器 2.5kWh/100km 2.1kWh/100km 16%
混合动力能量回收 85%效率 92%效率 7%提升
五、挑战与优化方向
成本控制:精密齿轮加工依赖进口设备,国产化后可降低25%-30%成本。
高温稳定性:开发耐150℃以上高温的合成润滑脂,避免效率衰减。
智能化升级:结合车联网数据预判路况,动态优化传动策略。
总结
汽车用行星减速机通过高效传动、轻量化、智能控制三大路径实现显著节能效果,尤其在新能源车领域,其综合节能贡献可达15%-20%。随着材料工艺突破(如渗碳合金钢)和智能化升级(AI动态调参),未来五年内单车能耗有望再降10%-12%。
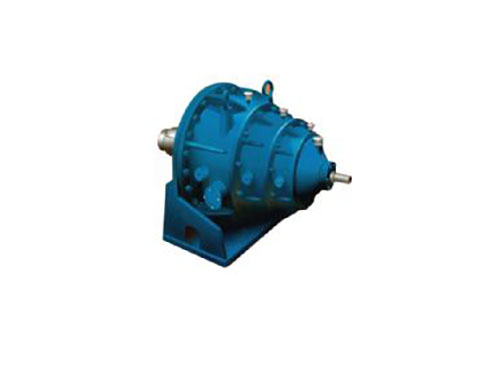